LSLT - 160 (Low Shrink, Low Temp) RP Production Molding Rubber 8 X 9 inch sheets
LSLT-160™ is made in America and designed to provide extremely low shrink (.64%) and low 160°F (71°C) cure capability, while maintaining very high tear resistance. Molds can be made from hard carved waxes without special pre-treatment with any kind of release agent. You need to use React-Shun RP dip with resin models to prevent bonding to this rubber however. Do not use with 3-D Systems, Inc. type Projet or VIsijet RP materials.
This rubber cures at 160oF 805oC. Most RP material for prototypes and engineering materials can handle that temperature. It is much cooler than the 350oF of regular silicone rubber. Of course you can use this rubber for metal models as well but why bother if you can directly print your models and make production molds from the print. You must dip resin RP parts in the React_Shun RP dip before packing them in any silicone molding rubber or it will bond and you will have a mess on your hands.
Since LSLT-160™ has a high affinity for aluminum and stainless steel mold plates, you should coat your mold plates and mold frames with React-Shun RP Dip with a small brush as the mold will adhere to the plates and frame if you don't. As an alternative you can use our Teflon adhesive sheets to cover your mold plates. To ensure ease of mold removal, be sure to coat the mold frame. Do not use silicone spray as it will retard the cure and will not prevent the rubber from sticking to the metal frame or plates.
American made low temperature, low shrinkage, vulcanized molding rubber sheets for larger molds. Used in conjunction with one dip in React-Shun RP dip, you can make direct production molds from your 3D printed parts or hard carving wax in an hour or so compared to 18 - 24 hours using most platinum catalyst liquid silicone rubber compounds. As a long time production mold cutter myself, the color of the rubber is important. The light green color of this rubber is easy on the eyes during precision cutting. Bright colors such as bright yellow, pink, or similar can quickly tire the eyes and the reflection from the required light to perform intricate cuts can easily lead to poor cuts and excessive parting lines on your injected waxes.
- Cure time per 1/4 inch (6.35mm) @ 160oF (61oC) 30 minutes
- Cure time per 1/4 inch (6.35mm) @ 250oF (121oC) 5 minutes
- Hardness: Shore A scale - 45
- Elongation - 750%
- Average shrink - 0.64%
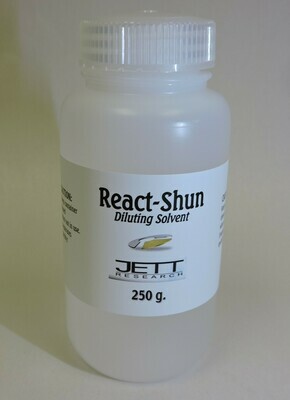
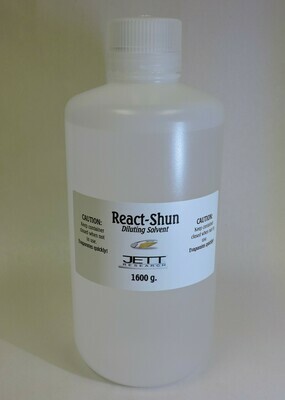